How to Prepare for a Welding Inspection Milwaukee Specialists Recommend
Wiki Article
Understanding the Value of Welding Examination in Ensuring Structural Honesty and Security Across Numerous Industries
Welding examination is an important procedure that safeguards structural stability and safety throughout varied markets. As we check out the ins and outs of welding assessment, the concern arises: what are the most critical variables that contribute to reliable inspection processes?Role of Welding Inspection
While the integrity of welded frameworks is extremely important to safety and security and performance, the function of welding assessment can not be overemphasized. Welding assessment functions as a crucial quality assurance process that guarantees the adherence to established standards and specs throughout the welding operation. By methodically evaluating welds for flaws, inconsistencies, and non-compliance, assessors play a crucial duty in guarding the integrity of frameworks throughout numerous sectors.Welding evaluations encompass a variety of activities, from pre-weld evaluations to post-weld examinations. These assessments not just recognize possible concerns before they escalate but additionally boost the general reliability and life-span of bonded parts. Welding Inspection Milwaukee. Evaluations aid to validate the ability and expertises of welders, making sure that welding procedures are carried out correctly and products are suitable
Furthermore, an extensive examination protocol promotes conformity with governing demands and sector requirements, lessening the threat of tragic failings. By advertising a culture of safety and security and responsibility, welding inspection adds considerably to both operational and financial efficiencies. In amount, the role of welding examination is indispensable, as it underpins the top quality, security, and longevity of bonded structures important to modern infrastructure and sector.
Types of Welding Assessments
Recognizing the different kinds of welding examinations is essential for preserving the top quality and safety and security of welded frameworks. Welding assessments can be categorized into several types, each offering a certain function in the evaluation procedure.Aesthetic assessment is one of the most essential kind, including a careful assessment of the welds with the naked eye or with magnification. This technique assists recognize surface problems such as fractures, incomplete blend, or too much spatter.
Next is non-destructive testing (NDT), that includes techniques such as ultrasonic testing, radiographic testing, and magnetic fragment screening. These techniques permit examiners to analyze the honesty of welds without compromising the material's framework. Ultrasonic screening utilizes high-frequency acoustic waves to discover interior defects, while radiographic testing employs X-rays or gamma rays to visualize inner weld characteristics. Magnetic bit testing, on the other hand, works for identifying surface area and near-surface discontinuities in ferromagnetic materials.
Damaging screening, though less typical, includes physically checking samples to recognize the weld's mechanical residential properties. Each type of inspection adds to a thorough assessment, ensuring that welding fulfills industry requirements and safety and security needs.
Industry Specifications and Regulations
Establishing market standards and policies is essential for ensuring the security and integrity of welded frameworks. These standards work as benchmarks for efficiency, high quality, and safety and security, directing makers and examiners in the execution of welding procedures. Various companies, such as the American Welding Culture (AWS) and the International Company for Standardization (ISO), have developed thorough criteria that dictate treatments for welding methods, certification of welders, and evaluation techniques.Compliance with these regulations not just enhances the quality of welds but likewise decreases dangers linked with structural failures. Particular codes, such as the ASME Central Heating Boiler and Stress Vessel Code, synopsis needs for the building and construction of pressure vessels, guaranteeing they can withstand functional anxieties. Additionally, nationwide and regional guidelines typically mandate adherence to these market standards, reinforcing their importance across sectors like building, aerospace, and vehicle manufacturing.
Normal updates to these criteria mirror innovations in technology and welding methods, guaranteeing that security procedures continue to be relevant. Thus, a detailed understanding and execution of these requirements is necessary for welding experts, fostering a society of security and top quality in welded structures.
Consequences of Poor Inspections
Poor evaluations can lead to serious repercussions in the welding market, undermining the extremely regulations and requirements designed to make sure safety and architectural integrity. The repercussions of poor assessments can manifest in numerous types, from immediate safety hazards to lasting architectural failures. Among one of the most disconcerting outcomes is the why not try this out potential for catastrophic accidents, which can result in substantial injury or death. In industries such as production, construction, and aerospace, the effects of subpar welding can endanger whole structures or parts, causing pricey repair services and comprehensive downtime (Welding Inspection Milwaukee).Moreover, insufficient evaluations can stain a company's track record and result in legal repercussions, including fines and lawsuits. Eventually, the implications of poor assessments prolong beyond specific tasks, affecting industry-wide criteria and public assumption, therefore stressing the important need for rigorous and reliable welding inspections.
Best Practices for Effective Inspections
Reliable welding assessments are extremely important to making certain the stability and security of bonded structures. To attain ideal results, assessors must abide by numerous best methods that improve the evaluation process.
Secondly, inspectors ought to possess the required credentials and certifications appropriate to the welding procedures and products being examined. Ongoing training and professional development are essential to staying upgraded on sector requirements and technological improvements.
In addition, making use of ideal evaluation tools and strategies, such as visual examinations, ultrasonic screening, and radiographic assessments, is crucial for identifying problems that could endanger architectural stability.
Finally, extensive paperwork of the inspection procedure is necessary. By implementing these ideal practices, organizations can significantly enhance the efficiency of their welding inspections and guarantee risk-free, reliable procedures.
Verdict

In final thought, welding evaluation is important for maintaining architectural honesty and safety and security throughout numerous industries. Focusing on reliable welding evaluations is vital to guarantee the safety and security of employees, possessions, and total operational honesty.
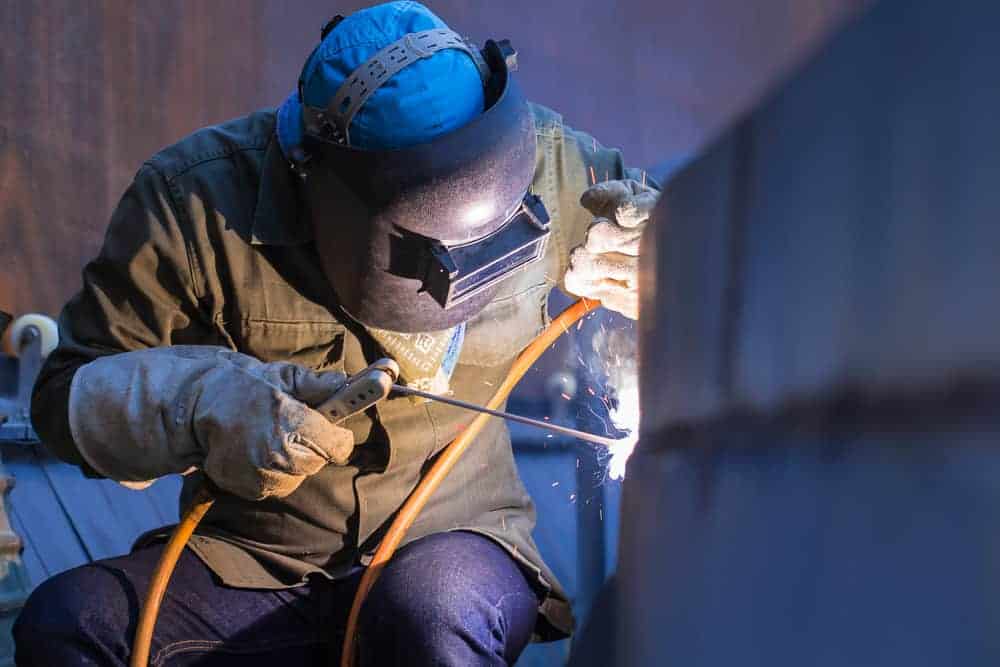
As we discover the ins and outs of welding examination, the inquiry arises: what are the most essential factors that add to reliable examination procedures?
Welding evaluation serves as an important quality control process that click this link makes certain the adherence to developed requirements and specifications throughout the welding procedure. In amount, the role of welding evaluation is indispensable, as it underpins the high quality, safety and security, and longevity of welded structures important to contemporary facilities and sector.
Numerous organizations, such as the American Welding Society (AWS) and the International Company for Standardization (ISO), have actually developed detailed criteria that determine treatments for welding practices, qualification of welders, and evaluation methods.
Eventually, the ramifications of poor examinations prolong beyond private jobs, influencing industry-wide criteria and public understanding, thus stressing the important requirement for rigorous and reliable welding inspections.
Report this wiki page